The Medical FEP Heat Shrink Tube is a vital enabler in modern healthcare, supporting safer, cleaner, and more efficient devices. From robotic surgery to diagnostics, FEP heat shrink tube plays a quiet but essential role in advancing patient care.
fep heat shrink tubing manufacturer
Forbest FEP Heat Shrink Tubing: Key Material for High-Performance Medical Equipment
In the field of medical equipment manufacturing, material selection is critical to product performance and reliability. Forbest’s FEP (Fluorinated Ethylene Propylene) heat shrink tubing, with its outstanding performance, has become the material of choice for numerous medical equipment manufacturers.
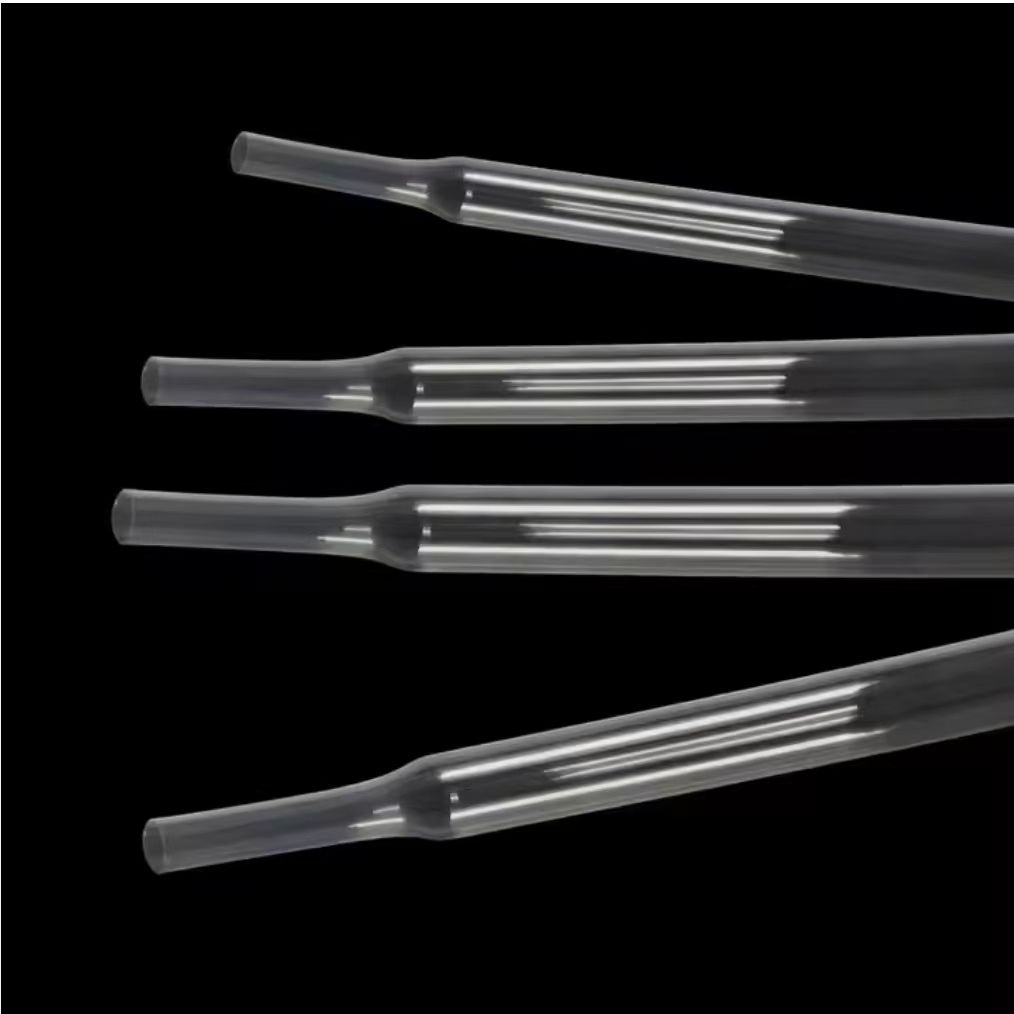
FEP Heat Shrink Tubing
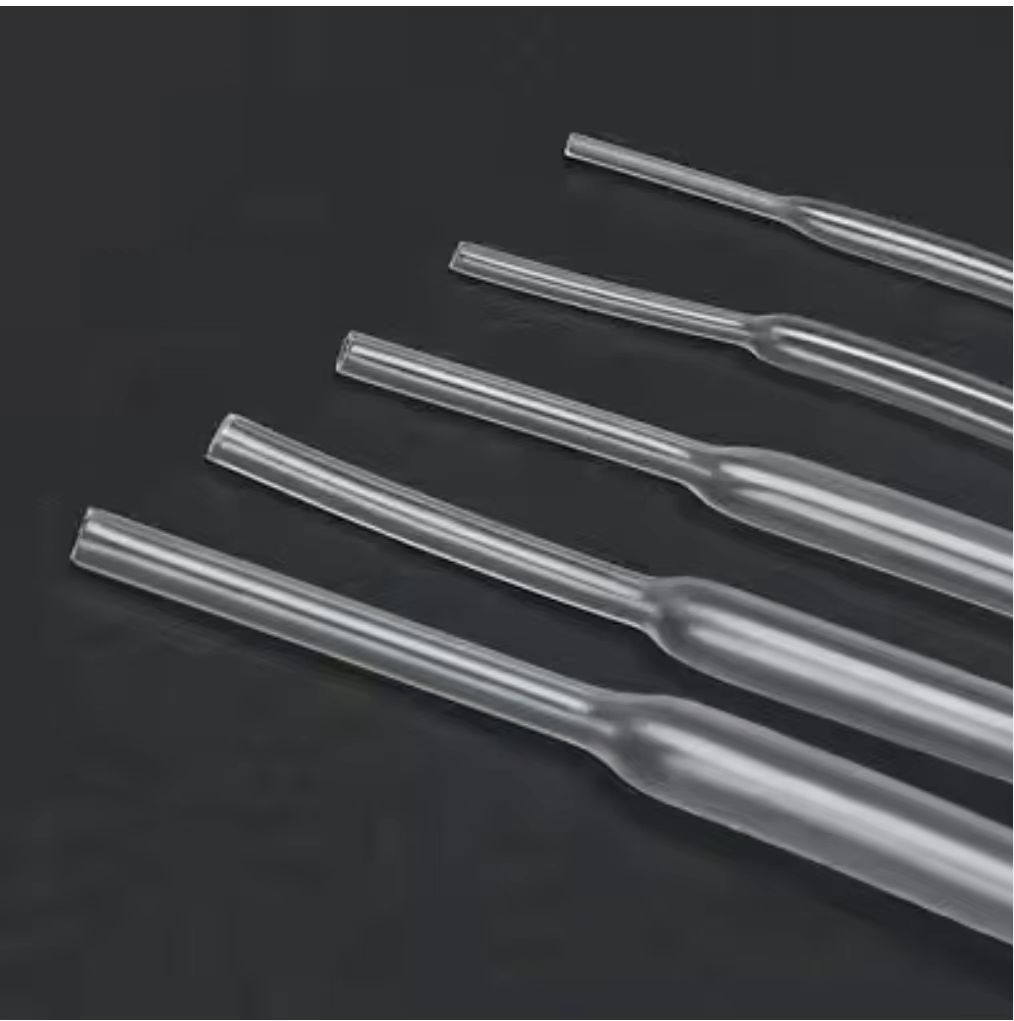
FEP Heat Shrink Tubing
Unique Properties of FEP Heat Shrink Tubing
FEP stands for Fluorinated Ethylene Propylene, and it’s a type of heat shrink tubing with unique properties. It has high chemical resistance, a wide temperature range, excellent transparency, and a low coefficient of friction. Additionally, FEP offers electrical insulation and non-stick qualities. This kind of tubing is specifically made from FEP polymer and is widely used for electrical insulation due to its durability and versatile characteristics.
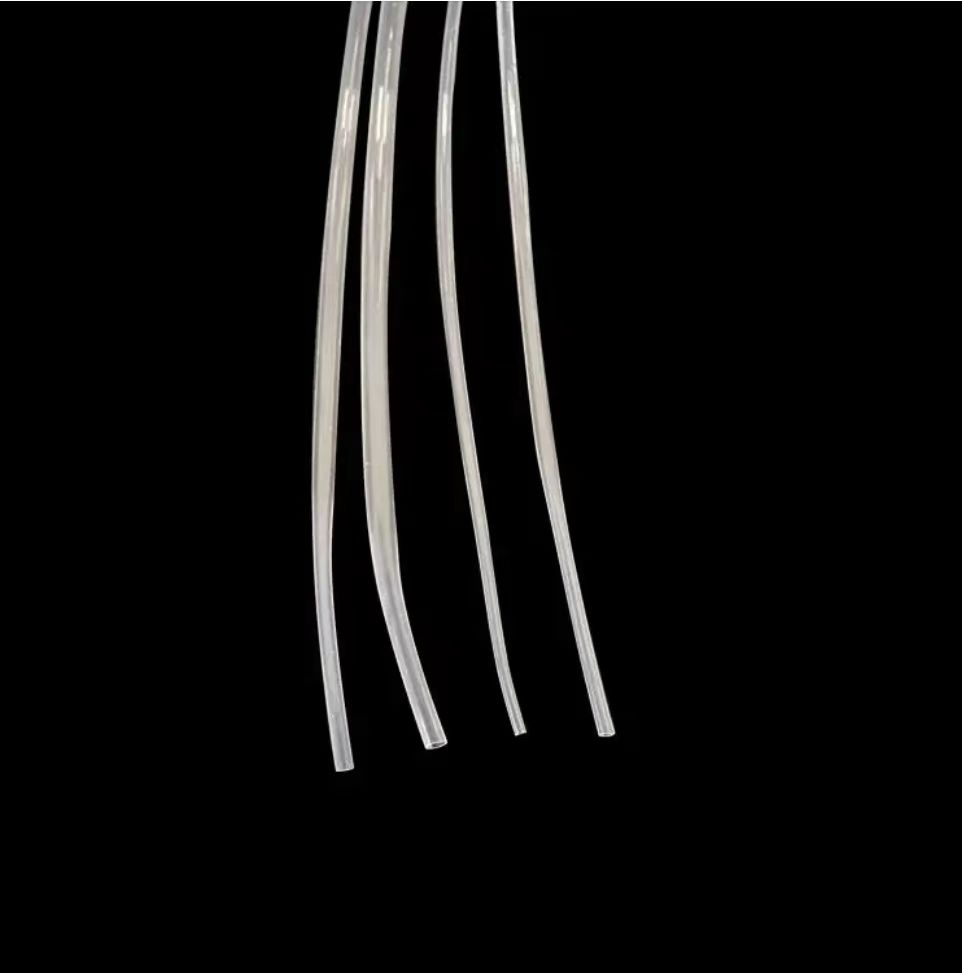
FEP heat shrink tubing material
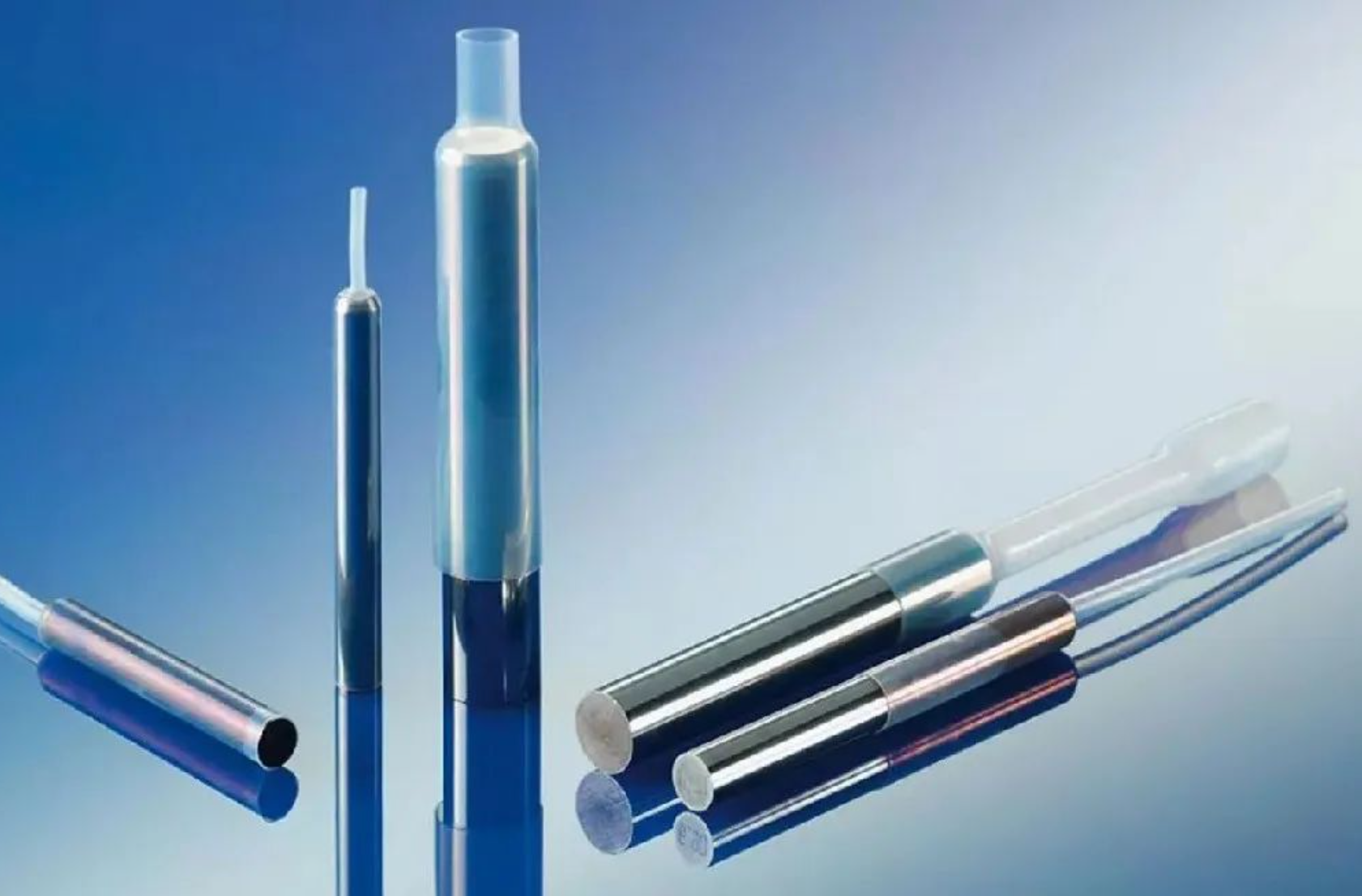
FEP heat shrink tubing medical equipment materials
Excellent Heat Resistance and Chemical Stability
Forbest’s FEP heat shrink tubing remains stable at temperatures up to 450°F (approximately 232°C), making it well-suited for high-temperature sterilization processes (such as autoclaving) and cleaning procedures. In addition, FEP material exhibits excellent resistance to a variety of chemicals, including common disinfectants and solvents.
Low Shrinkage Temperature and High Transparency
The shrinkage temperature of FEP heat shrink tubing is relatively low, typically around 210°C (410°F), which ensures that sensitive components are not damaged during installation. Additionally, the high transparency of FEP material makes it ideal for medical applications that require visual inspection, such as catheter manufacturing and endoscope equipment.
Surface Lubricity and Low Friction Coefficient
FEP heat shrink tubing features excellent surface lubricity, reducing friction during device operation and thus enhancing smoothness and patient comfort. This low friction coefficient makes it especially suitable for use in interventional medical devices.
Customized Solutions
In today’s fast-paced world, one size doesn’t fit all. That’s why we offer tailor-made FEP heat shrink tubing solutions designed to meet your unique needs. Whether you’re in aerospace, medical, electronics, or chemical processing, we can adjust sizes, shrink ratios, colors, and more to perfectly fit your project. We work closely with you—from design through production—to deliver high-performance products that keep your systems running smoothly.
Diverse Sizes and Shrink Ratios
Forbest offers standard FEP heat shrink tubing sizes with shrink ratios of 1.3:1 and 1.6:1. Customization services are also available, with shrink ratios reaching up to 1.8:1. This variety ensures that different medical device requirements can be precisely met.
Silicone-Free Manufacturing Process
To ensure product purity and biocompatibility, Forbest’s FEP heat shrink tubing is manufactured using a silicone-free process. This process prevents potential contamination from silicone-based substances, thereby enhancing the overall quality of the product.
Application Areas
FEP heat shrink tubing is widely used in medical devices, including but not limited to the following areas:
- Catheter Manufacturing: Provides a protective layer for catheters, ensuring their integrity during high-temperature sterilization.
- Endoscopic Equipment: Protects internal components while providing transparency for visual inspection.
- Electrical Insulation: Offers reliable electrical insulation for the electrical components in medical devices, ensuring safe operation.
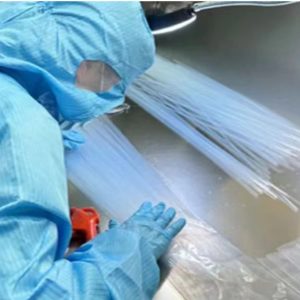
FEP heat shrink tubing manufacturing
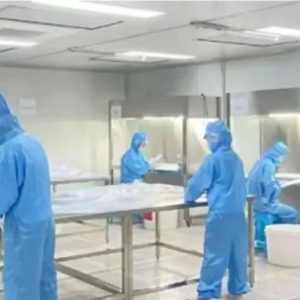
FEP heat shrink tubing manufacturing
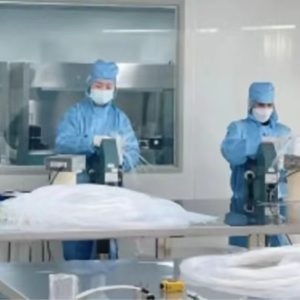
Production of FEP heat shrink tubing
Conclusion
Forbest’s FEP heat shrink tubing, with its outstanding heat resistance, chemical stability, low shrinkage temperature, and high transparency, is the ideal choice for the medical equipment manufacturing industry. By offering customized services, Forbest can meet the specific needs of different customers, ensuring that its products perform excellently in various complex applications.
What is the difference between PTFE, FEP, PFA, and ETFE?
Teflon PTFE: Teflon PTFE: Teflon PTFE: Teflon PTFE: Teflon PTFE: Teflon PTFE: Tefl The non-stick coating PTFE (polytetrafluoroethylene) may be used continuously at 260°C, with a maximum operating temperature of 290-300°C, and has a very low friction coefficient, excellent wear resistance, and chemical stability.
Teflon FEP: A non-stick coating made of FEP (fluorinated ethylene propylene copolymer) that melts and flows during baking to form a non-porous film with great chemical stability, outstanding non-stick qualities, and a maximum service temperature of 200 degrees Celsius.
PFA (perfluoroalkylate) non-stick coatings melt and flow when baked to generate a non-porous film similar to FEP. PFA has the advantages of a higher continuous usage temperature of 260° C, greater rigidity and toughness, and is particularly well suited to anti-sticking and chemical resistance under high temperature settings.
ETFE (ethylene-tetrafluoroethylene copolymer): ETFE is an ethylene-tetrafluoroethylene copolymer. This resin is the toughest fluoropolymer, capable of forming a long-lasting coating with exceptional chemical resistance and continuous use at 150°C.
PFA hose is extremely durable and resistant to wear
PFA hose is long-lasting and resistant to wear. It is a copolymer of perfluoropropyl perfluorovinyl ether and polytetrafluoroethylene with a small amount of perfluoropropyl perfluorovinyl ether. When compared to PTFE, melt adhesion is improved, melt viscosity is reduced, and performance is unchanged. This resin can be directly molded into products using standard thermoplastic molding techniques.
2. The long-term use temperature of PFA pipe is -80–260 degrees, and it has excellent chemical corrosion resistance, corrosion resistance to all chemicals, good electrical properties in plastics, and its electrical insulation is not affected by temperature. Influence, dubbed the “Plastic King.”
3. PFA pipe has a higher creep resistance and compressive strength than PTFE pipe, a higher tensile strength, and an elongation rate of 100-300 percent. Excellent radiation resistance and good dielectric properties.
PFA pipes have a variety of properties.
In addition to being used to make pipes, PFA pipe material has many other applications as a special material, particularly cold-resistant PFA. In fact, it has the same application field as PTFE, but it can form products with more complex shapes than PTFE.
Aside from the well-known PFA tube, another common one is the PFA heating wire. The conductor is a resistance wire wound outside the tube that can heat up when energized. PFA heating wire is better suited for short-distance pipe heating, while long-distance pipe heating consumes a lot of energy due to voltage drop.
In general, PFA plastic pipe outperforms other products because it retains PFA’s excellent chemical stability, mechanical properties, electrical insulation, self-lubrication, non-stickiness, non-flammability, and aging resistance, among other benefits.
Furthermore, PFA plastic pipes have good high temperature stability, softness, resistance to cracking, and crack resistance. They can be used in a variety of situations, produce good results, and help to extend the service life of the pipe.
When comparing the PFA plastic pipe to the metal pipe, it is discovered that the PFA plastic pipe has a significant energy saving effect. Based on PFA plastic pipe production per cubic meter and steel and aluminum production per cubic meter, the energy consumption of steel is 316KJ/m3, and the energy consumption of aluminum is 316KJ/m3. The energy consumption is 619KJ/m3, while the pfa plastic pipe consumes 70KJ/m3.
How to tell if a PFA plastic pipe is good or not
When we were shopping for plastic pipes, merchants recommended PFA plastic pipes to us, but many people are unaware of what this PFA plastic pipe is. To understand PFA plastic pipe, we must first understand its raw material, which is a copolymer of perfluoropropyl perfluorovinyl ether and polytetrafluoroethylene.
As a result, in terms of evaluating the performance of PFA plastic pipe, other than its improved melt adhesion and reduced melt viscosity, there is no way to compare it to PTFE. Ordinary thermoplastic molding methods, which are very simple, are used to create PFA plastic pipes.
In general, PFA plastic pipe is superior to other products because it retains PFA’s excellent chemical stability, mechanical properties, electrical insulation, self-lubrication, non-stickiness, non-flammability, and aging resistance, as well as many other excellent properties.
. Furthermore, PFA plastic pipes have good high temperature stability, softness, crack resistance, and crack resistance. They can be used in a variety of situations, provide good results, and help to extend the service life of the pipe.
When comparing the PFA plastic pipe to the metal pipe, it is discovered that the PFA plastic pipe has a significant energy saving effect. Based on PFA plastic pipe production per cubic meter and steel and aluminum production per cubic meter, the energy consumption of steel is 316KJ/m3, and the energy consumption of aluminum is 316KJ/m3. The energy consumption is 619KJ/m3, while the pfa plastic pipe consumes 70KJ/m3.
PFA insulating sleeve value and PFA corrugated pipe selection
PFA, as a widely used plastic material, can be transformed into a variety of products. Two examples are environmentally friendly PFA insulating sleeves and PFA corrugated pipes. They have different properties and applications, but the premise is that the quality of the pipe must be up to standard, and poor quality products will cause significant harm.
Not only does this environmentally friendly PFA insulating sleeve have soft elasticity, but it also has good flame retardancy, insulation, and temperature resistance. It has been widely used in the insulation protection of various wiring harnesses, solder joints and inductors, as well as the rust prevention of metal pipes and rods.
Because of its excellent corrosion resistance, the environmentally friendly PFA insulating sleeve is resistant to all chemicals and has a low coefficient of friction among various plastics. What’s more, the environmentally friendly PFA insulating sleeve has good electrical properties and electrical insulation that isn’t affected by temperature.
Furthermore, the creep resistance and compressive strength of environmentally friendly PFA insulating sleeves are superior to those of PTFE, as is the tensile strength. In a nutshell, the environmentally friendly PFA insulating sleeve is a near-perfect product. Let us now discuss PFA bellows.
What is the difference between PTFE and PFA?
PFA is translucent, while PTFE is pure white and opaque. Temperature resistance: PFA -200°C to +260°C, PTFE -200°C to +250°C.
PFA is a granular raw material, whereas PTFE is a powder. Polytetrafluoroethylene (PTFE): Polytetrafluoroethylene (Poly tetra fluoroethylene, abbreviated as PTFE), also known as “nonstick coating” or “easy-to-clean material.” This material is resistant to acids and alkalis, as well as various organic solvents, and is nearly insoluble in all solvents. At the same time, polytetrafluoroethylene has high temperature resistance and an extremely low friction coefficient, making it suitable for lubrication. It has also become an ideal coating for easy cleaning of the inner layer of water pipes.
PFA plastic is a copolymer of perfluoropropyl perfluorovinyl ether and polytetrafluoroethylene. When compared to PTFE, melt adhesion is improved, melt viscosity is reduced, and performance remains unchanged. This resin can be directly processed into products using standard thermoplastic molding techniques. Suitable for corrosion-resistant parts, anti-wear parts, seals, insulating parts, and medical device parts, high-temperature wire and cable insulation, anti-corrosion equipment, sealing materials, pump valve bushings, and chemical containers. It is a copolymer of perfluoropropyl perfluorovinyl ether and polytetrafluoroethylene. When compared to PTFE, melt adhesion is improved, melt viscosity is reduced, and performance remains unchanged. This resin can be directly processed into products using standard thermoplastic molding techniques.
Temperature range of -196–260 degrees Fahrenheit for long-term use
Long-term use temperature of -196–260 degrees, excellent chemical resistance, corrosion resistance to all chemicals, the lowest friction coefficient among plastics, and good electrical properties; its electrical insulation is unaffected by temperature. The “Plastic King” is its nickname. It has chemical resistance comparable to PTFE but superior to vinylidene fluoride. It has higher creep resistance and compressive strength than PTFE, as well as a high tensile strength and elongation of 100-300 percent. Excellent radiation resistance and good dielectric properties. The flame retardancy has been increased to V0. It can be used to make corrosion-resistant parts, anti-friction wear parts, sealing parts, insulating parts, and medical equipment components. Insulation for high-temperature wires and cables, anti-corrosion equipment, sealing materials, pump valve bushings, and chemical containers
Teflon’s performance characteristics and applications
After extrusion and sintering, drying, high temperature sintering, shaping, and other procedures, Teflon (sleeve) pipe is an unique pipe manufactured of polytetrafluoroethylene (PTFE also known as Teflon, plastic king). PTFE, often known as Teflon in English, is a material that is widely utilized in machinery, electronic appliances, autos, aerospace, chemicals, computers, electric heating, military, communications, and other essential technology industries, including micro-transformers.
Features
1. Chemical stability: can withstand the impacts of strong acids such as aqua regia, hydrofluoric acid, concentrated hydrochloric acid, nitric acid, oleum, organic acids, and other strong acids, as well as strong bases, strong oxidants, reducing agents, and various organic solvents. Ideal for chemical feeds with high purity.
2. Low friction coefficient: the friction coefficient is often less than 0.04, making it a great self-lubricating material that does not vary as temperature changes.
3. The inner wall of the tube has excellent anti-adhesion properties, making it difficult for colloids and chemicals to attach to it.
4. Excellent aging resistance; can be left outside for extended periods of time.
5. Excellent electrical insulation: PTFE is a non-polar substance with good dielectric characteristics, a high resistance, and a dielectric constant of around 1.
FEP Heat Shrinkable Tubing introduction
FEP heat shrinkable tubing
Name of the product Heat shrinkable tube made of polyperfluoroethylene propylene (F46, FEP).
parameters of performance: No leakage, low friction coefficient of kinetic friction, 0.2-0.3, non-stick, water, oil-water contact angle=114o, non-flammable air will not burn (oxygen index >95VOL percent), shrink ratio is 1.3:1,1.6:1.
Features Heat-shrinkable tube made of temperature-resistant polyperfluoroethylene propylene (F46, FEP)—200°C Heat-shrinkable tube made of fusible polytetrafluoroethylene (PFA)—200—250°C At high temperatures, only elemental fluorine and alkali metals resist corrosion. It works with it and has no effect on any other inorganic organic acids, alkalis, or esters, whether concentrated and dilute.
Application Teflon FEP heat shrinkable tube has excellent wear resistance, chemical corrosion resistance, and high temperature performance. It is utilized for insulation protection and pressure relief at connection welds, as well as the differentiation and identification of coated components.
what is PFA Film
PFA film is a transparent, thermoplastic film that can be heat sealed, thermoformed, vacuum formed, heat bonded, welded, metallized, laminated (combined with dozens of other materials), and used as an excellent hot-melt adhesive.
Extrusion or blow molding are used to create PFA film from tetrafluoroethylene and perfluoropropyl vinyl ether copolymer resin. It has excellent high and low temperature resistance, chemical corrosion resistance, high insulation, non-stick properties, and light transmission. In the temperature range of -80 to 200°C, it can be used for a long time. High and low temperature resistance, twice as high as F4, non-stick, high insulation, can be exposed to ozone and sunlight for an extended period of time
fep heat shrink medical tubing market
The revenue from FEP heat shrink medical tubes is expected to reach USD 103 million in 2019 and USD 146 million by 2024. Microcatheters and surgical instruments use FEP heat shrink medical tubing, which is in high demand. Chemically inert, moisture resistant, and temperature resistant, FEP is a great choice. FEP is also suitable for surgical instruments and microcatheters because it can be extruded with thin walls.
Between 2019 and 2024, drug delivery devices are expected to be the fastest-growing application of the FEP heat shrink medical market.
The use of microcatheters in minimally invasive surgical procedures has increased demand for FEP heat shrink medical tubes in medical devices, owing to an increase in the geriatric population and an increase in the number of chronic diseases.
As a result of the application:
Drug distribution (Catheter)
Instruments for surgery and vascular surgery
Joints that are flexible (Shafting)
Others who deal with electrical insulation